Action Generator turns mechanical energy into electricity that can be used to power home, business or industry. These appliances are crucial during a power outage.
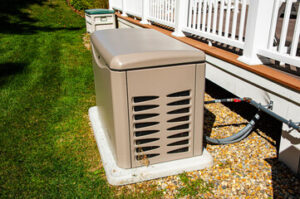
Early generators like Hippolyte Pixii’s dynamo relied on mechanical rotation to turn the coils and magnets and create electric potential. This design was inefficient and produced counterflows of current on the copper disc, limiting power output.
Whether used to provide backup power during an outage or to help equipment that runs on electricity operate in remote locations, a generator can make all the difference for a family, business, or institution. The generator is a machine that converts mechanical energy into electrical energy by forcing electrons into an electric circuit at a fixed frequency to induce current and produce electricity.
While some large-scale electrical generators use hydroelectricity to create power, residential and commercial generators rely on fuel sources like gas, diesel or propane to create the mechanical energy that can be turned into electricity. The key is that the generator must be able to produce a great deal of electricity for long periods of time, so it must have an engine and alternator that are designed to work together.
Most generators today are designed to run at a power factor of 0.8, the industry standard. This means that the generator can produce a large amount of power while still maintaining an excellent level of efficiency. Power factors lower than 0.8 reduce the electrical distribution capacity of a generator, leading to energy inefficiency and large kVA ratings that are costly for businesses to maintain.
The generator works by creating a magnetic field around a group of wound coils that generates electrons, which are then pushed along by the engine. The number of electrons that are pushed along by the magnetic field is called current and is measured in amps, while the “pressure” pushing them along is measured in voltage.
A generator’s ability to create a great number of electrons for a long period of time is also known as real power, and it is calculated in kilowatts. Real power is the type of power that performs work, while reactive power is the power that overcomes the magnetic force to move electrons.
The generator is powered by a internal combustion engine, which is often connected to an alternator that generates alternating current at a fixed frequency (usually 50 or 60 cycles, or double reversals, per second). Most of the generators used to supply electric power networks are synchronous generators and are known as alternators as well.
Efficiency
The generator is a machine that converts mechanical energy into electrical energy. This mechanical energy may come from coal- or steam-powered turbines at dams or waterfalls, natural gas turbines powered by combustion of fossil fuels, nuclear fission, wind or solar panels. The generator converts the mechanical energy to electrical energy by using the rotational speed of the engine turning the shaft, and the magnetic forces generated by rotating electromagnetic field coils in the stator, to generate electricity.
Electricity generated by the generator is in the form of alternating current. The magnitude of this alternating current will vary with the speed of the generator, which is why a voltage regulator helps to stabilize power output. The alternating current is used for transmission over long distances, and it is transformed to low voltage and low current at each consumer’s outlet by transformers.
A generator is a very useful device during power outages. It provides a source of energy for appliances, and also ensures that food, medications and other supplies will not be damaged or lost due to lack of refrigeration. It also allows businesses to continue operations, and prevents disruption of daily activities or loss of revenue.
The simplest way to think about the mechanics of the generator is that it acts like a pump pushing water through a pipe. The magnet in the generator pushes electrons along, and the water pumps them through a pipe. This analogy is a bit oversimplified, but it helps to understand the principles at work.
Electrostatic generators were extremely inefficient and had no practical use, but they demonstrated that magnetism could be used to create electrical power. It was a significant step that opened the door to commutators, direct current dynamos and finally to current alternators.
The main components of the generator are the genhead and fuel system. The genhead is the assembly of stationary and moving parts that encases the engine in a housing. The rotor is the moving part that spins in the stator, creating relative movement between the magnetic and electric fields. The stator is the stationary component that contains a set of electrical conductors wound in coils over an iron core.
Design
Power generators use the principle of electromagnetic induction discovered by Michael Faraday to generate electricity. A conductor coil of copper, called an armature, is placed inside a magnetic field created by a set of conducting coils known as field windings. When the generator’s engine starts up, mechanical energy is used to force the movement of electric charges present in the wires of its armature through an external electrical circuit, thus generating electric current. The armature’s motion induces a rotational magnetic field in the iron core of the generator that then creates electric currents that flow through the armature and out of its terminals to generate electricity.
The generator’s control panel is responsible for regulating the outputs of the engine. Its gauges measure essential parameters such as oil pressure, coolant temperature, battery voltage and engine rotation speed among others. Constant measurement and monitoring of these parameters allows for built-in shutdown of the generator when these variables exceed their respective thresholds.
It also regulates the output of the generator by taking a small portion of its AC voltage and converting it to DC current using a set of secondary windings known as exciter windings. These are connected to units known as rotating rectifiers that then convert the DC current back into an AC voltage. The output of the rotor / armature then generates an electromagnetic field that in turn induces a larger AC voltage across the stator’s coils, producing more electricity for the generator.
Generators come in different sizes and power capacities that allow a wide range of users to match their specific requirements to the right model for them. They can be powered by a variety of sources including gasoline, natural gas, LPG or diesel fuel. These models are designed to provide power for residential and commercial structures. Some can also be fueled with alternative energy sources like solar energy or wind power. These units are also available in portable or stationary designs. They vary in size and weight but they are usually mounted on a customized frame to support their structure and facilitate mobility.
Maintenance
A generator is a crucial piece of equipment for businesses that need to keep working in case of an emergency. But it’s easy for the generator to fall into disrepair without regular inspections and servicing. This may lead to expensive and time-consuming repairs, or even system failure if the problem isn’t addressed quickly. By regularly inspecting the generator and following a routine maintenance schedule, minor issues can be identified early and addressed while they are still cost-effective.
Inspect the fuel system with the generator running to ensure there are no leaks or other problems. Also, the air intake and exhaust system should be inspected on a daily basis to ensure they are not damaged or clogged. The air cleaner filter elements should be cleaned or replaced as necessary based on the conditions in which the generator sets operate. Also, the charge-air piping should be checked for cracks or holes and the hoses should be tightened.
The lubrication for the generator should be inspected and changed on a weekly basis if it’s being used for long periods of time. This helps prevent damage to the generator from a lack of proper lubrication, which can cause it to overheat or fail.
In addition to these checks, it’s a good idea to perform load bank testing and a confidence test on the generator on a regular basis. This helps prevent the buildup of excess fuel in the engine and improves its performance during emergencies.
A routine maintenance schedule for a generator can be divvied up into short weekly self-inspections, more detailed monthly self-inspections, and technician visits on a bi-annual or yearly basis. Each plan should be based on the specific application and the needs of the business. The schedule should include tasks such as checking the battery charge rate, monitoring fuel levels, examining power systems for signs of faulty wiring, and performing fluid analysis. The schedule should be created using work order software to help streamline the process. This can help to save time and money by automating some of the more mundane tasks. It can also help to keep track of changes and prevent duplicated efforts.